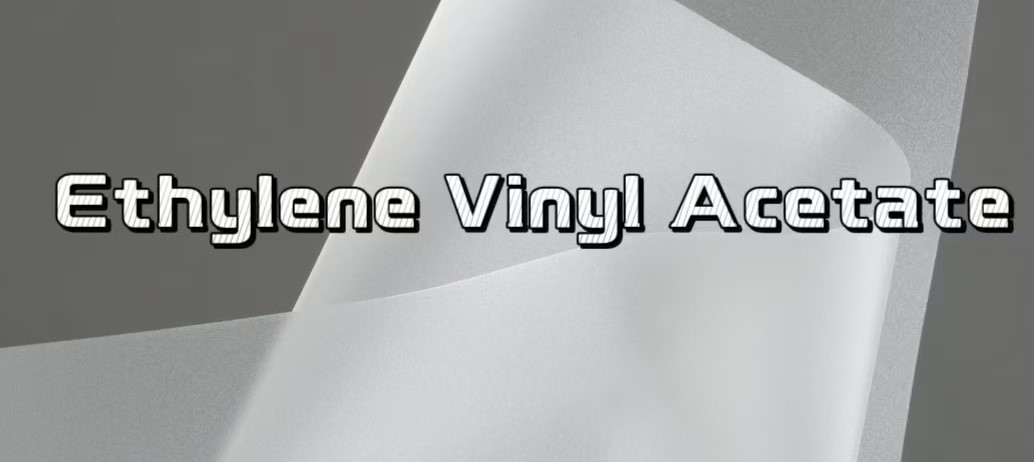
The high strength, high fluidity and small size effect of fumed silica are used to improve the toughness of the material without reducing the rigidity of the material, and at the same time improve the density, smoothness, wear resistance, rigidity and other capabilities of plastic products. Through appropriate surface modification, the purpose of simultaneously strengthening and toughening plastics can be achieved. Adding fumed silica to polyethylene, through a special method, the silica can be evenly dispersed in the matrix to produce a polyethylene composite material with high wear resistance and high hardness.
The use of fumed silica to transmit light and small particle size can make the plastic compounds denser. Adding silica to the polystyrene plastic film not only improves its transparency, strength, and toughness, but also significantly improves its waterproof and anti-aging properties.
Adding fumed silica to epoxy resin can significantly improve its brittleness. It can overcome the defects of reduced material rigidity and strength caused by the toughening of elastomers, and achieve the purpose of strengthening and toughening. If nanosilica is modified by a coupling agent, its impact toughness can be increased by around more than one time and its tensile properties can be increased by 30%. In addition, the hardness, wear resistance, temperature resistance, insulation and other properties of the product can also be improved.
After modifying ordinary plastic polypropylene, the main technical indicators (water absorption, insulation resistance, compression residual deformation, flexural strength, etc.) have reached or exceeded the performance indicators of engineering plastic nylon fiber, realizing the use of polypropylene railway accessories instead of nylon 6, product costs dropped significantly.
Recommended grades: HJSIL 200